Case Study: Crown Stair
The A400 Brings 70-75% Greater Efficiency
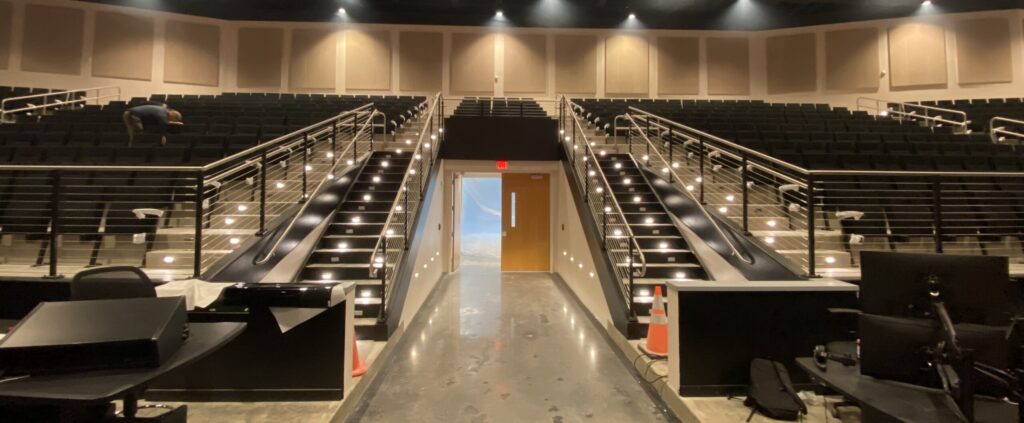
John Spirek started Crown Stair in 2000 as a distributor of shop-built wood stairs for residential properties. Over the last several years, the company has embraced a new direction — specializing in custom metal fabrication for stairways and railings.
During the early years of their metalworking operations in Lexington, Kentucky, Crown Stair relied on MDF templates and manual punching for C-channel and flat bar components. The company performed many other tasks manually, including coping round tube posts and mid-bars, laying out bend locations and cutting and fitting every baluster for commercial rails. These manual methods were time-consuming and prone to errors and inconsistencies. After adding the Bend-Tech A400 to the shop, Crown Stair is now able to automate tasks and take on more work to grow the business.
Discovering the A400 Through NOMMA
Crown Stair’s journey to automation took a major step forward after joining the National Ornamental & Miscellaneous Metals Association (NOMMA). Through NOMMA’s publications, they were introduced to new tools and technologies that piqued their interest and offered options to take their metalworking to the next level.
Josh Dodson, Metal Shop Coordinator and Salesman at Crown Stair, first saw the Bend-Tech A400 at FABTECH 2022. He and his team watched the equipment in action and met the Bend-Tech team. This in-person experience was a turning point for Dodson, sparking his interest and furthering discussions that eventually led to the purchase of the A400.
What ultimately set Bend-Tech’s A400 apart from other options for CNC tube and pipe plasma cutters was the approach taken by Bend-Tech — developing user-friendly software first and then designing a machine to work seamlessly with it. Dodson wanted a machine that was designed to be versatile and easy for his team to use. Bend-Tech made the designing, programming and operation process intuitive. The simplicity and usability of the platform eliminated a major hurdle and motivated the Crown Stair team to move forward with the A400.
Bend-Tech Helps Eliminate Costs
Crown Stair revolutionized their fabrication process with the A400. It was Crown Stair’s first CNC tube and pipe cutter, brought in to automate and simplify the parts cutting process for commercial breezeway stairs and railings. Before the A400, bending round tube required manual calculations and precise setup by skilled technicians, driving up labor costs, wasted material and slowing production. According to Dodson, “We used to have to make templates for each job which cost $100-300 per job. Now that we have the A400 and the marking abilities, that totally eliminated that cost.”
The A400 streamlined programming and verifying parts. And it was easy to incorporate the new processes into production. Initial on-site training from the Bend-Tech team helped Crown Stair’s A400 operators become so well-versed in the tools and technology that training new team members on the machine is now a process they do internally.
Cutting Operations Doubled
Unlike before, Crown Stair can directly cut baluster holes into tubing thanks to the A400. This allows everything to key together seamlessly without relying on templates. Components are cut slightly longer and then slotted using the machine’s slot and tab feature, ensuring a precise and accurate fit. This transformation sped up the assembly process, minimized the need for precision fitting and reduced questions and errors on the shop floor.
“Our metal fab division is 70-75% more efficient in pre-assembly (parts cutting, bending, layout) than it used to be with our manual process. The time saved has allowed us to take on more and more jobs."
This shift also eased the hiring requirements. Crown Stair can now focus efforts on fabrication rather than finding enough skilled workers to prep and cut parts manually. This, in turn also improved quality and efficiency farther down the production line. The result was a more streamlined workflow and a major boost in overall productivity. Dodson estimates that cutting operations have doubled with the A400, citing the machine for allowing Crown Stair to take on additional jobs they couldn’t do manually. The company will soon be moving into a new facility in Midway, Kentucky, to accommodate the growing business.
“Overall, the A400 has opened a lot of doors and saved us a ton of time and money."