Case Study: Goat Built
In-House Production Maximizes Profit
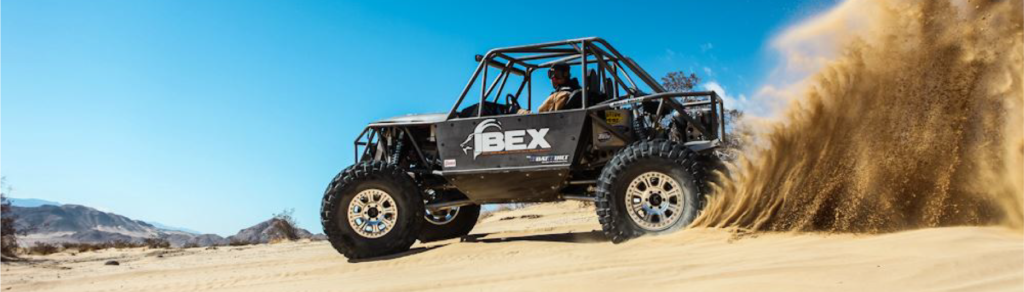
About Goat Built
Goat Built Design and Engineering is a leading manufacturer of weld-it-yourself tube kits for full-size, off-road, rock crawler chassis. With over 15 years of rock crawling, racing, and off-road industry design and manufacturing experience, Goat Built’s engineers are innovators committed to driving the industry forward.
The A400 Impact
Drew Burroughs, the founder of Goat Built, emphasizes accuracy in part production and design, and how it is essential for the customer to successfully weld a kit together. Formerly, this required outsourcing to a shop with a tube laser processing system, and Goat Built would have to wait for bulk orders to come in before they could purchase production of 6-10 chassis kits at a time.
Thanks to the A400, Goat Built can now build chassis one by one. The ability to manufacture in-house not only streamlines production efficiency, but also maintains production quality. Burroughs states:
“(The A400) has eliminated a 6-week lead time on part manufacturing by eliminating the outsourcing of manufacturing. Now, we can do single orders with custom pieces since production is 98% in-house.”